Gas Detection FAQs: Your Guide to Common Questions
Get answers to the most common gas detection questions.
What is gas detector calibration and why does it matter?
To ensure your gas detector can accurately detect gas levels, you must first calibrate it. Calibrating a gas detector means exposing it to a known calibration gas concentration or test gas for a specific amount of time. This reading becomes the gas detector’s reference point for future readings. Repeat this process each month to ensure accurate readings. Remember, you need to calibrate your gas detector regularly because sensors can drift over time, and poisons and inhibitors can affect gas readings.
You can calibrate your gas detector manually with calibration gas and some tubing, or you can use a docking station to automatically calibrate your monitor on a set schedule. Calibrating your gas detector with a docking station also allows you to access past calibration records and generate calibration certificates for compliance purposes.
Using incorrect or expired calibration gas can lead to an improper calibration, meaning your gas detector won’t display accurate readings. This simple mistake can have life-altering consequences, so it’s important to always check the contents and expiration dates of your calibration gas bottles. Once a bottle is expired, you should not use it because chemical reactions can take place inside the container and alter the contents.
What is a bump test and why does it matter?
Bump tests, also known as functional tests, protect you on the job by ensuring that your gas monitor will alert you to harmful levels of gas. In bump testing, the sensors in your gas detector are briefly exposed to a concentration of gas that is higher than the alarm’s set points. This test verifies that the sensors on your gas detector will respond and an alarm will go off as expected. It is important to note that bump testing does not check the accuracy of the gas reading—it just checks that the sensors and alarms are working. The only way to know that your gas detector works is by bump testing it before each shift.
The easiest way to bump test your monitor is with a docking station. The docking station can automatically bump test your gas detector on a set schedule before each shift. This eliminates the time and hassle of manually bump testing your monitor. If a docking station is not available, you can also manually bump test with calibration gas. Whichever method you choose, commit to doing it every day.
How often do I need to zero my gas monitor?
As a best practice, we train instrument users to perform four basic steps in clean air each time they turn their monitor on for use:
- Verify the battery charge level
- Zero the monitor
- Bump test
- Clear the peaks
You should never zero your gas detector unless you know that you are in a clean air environment. Zeroing a device in a contaminated atmosphere can lead to confusion in the resulting readings, and may even mask the readings of potentially dangerous gas concentrations.
If clean air is not available—as is common near fires or in smoky areas—you should use zero air (compressed air with impurities removed) to establish a baseline for your monitors. Zero air will not harm your monitors or disrupt sensor function.
If you turn on your Industrial Scientific gas monitor and the readings are within acceptable limits, there is no need to zero your monitor.
How do I know if my gas detectors are being used correctly?
Gas detectors only serve their purpose if people use them correctly. Without visibility into how people use gas detectors, you can’t know whether they serve their intended purpose. Beyond that baseline, you also need visibility into which alarms are going off, where, and for whom so you know when to intervene and stop unsafe behaviors. Identifying these trends is critical—but it can be nearly impossible with old-school, manual tools.
To get updates on critical alarm events, usage patterns, and maintenance needs, you will need a cloud-connected docking station paired with gas detection management software. With these additional tools, you can customize your reports for what matters most to you and view them on a simple dashboard for immediate insight into critical safety patterns. By pulling alarm and usage history out of your gas detectors and into a dashboard, you can see how your people use gas detectors and whether they are making safe choices.
How do I safely test the atmosphere for gas hazards before entering a confined space?
Regulations generally require testing the atmosphere within a confined space with a direct-reading monitor before a person enters.
Gas detectors with sampling pumps and a length of flexible tubing or a probe are ideal for drawing remote samples from confined spaces before entry. These samples are a critical step and must be recorded on a confined space entry permit.
During pre-entry sampling, use the 2x2 rule. This rule states that when using a sampling pump, you should wait two minutes plus two seconds for every foot of tubing. If you have 20 feet of tubing attached to your monitor, you would first wait two minutes, then add two seconds for each of those 20 feet, equalling 40 seconds. In this case, you would need to wait two minutes and 40 seconds for the most accurate reading.
Repeat this process at the top, middle, and bottom of the space because different gases settle at different heights, depending on their weight relative to air.
Regulatory agencies around the world have different minimum safe levels for entry, so you should always check with your local agency.
How do I continuously monitor gas hazards in a confined space throughout an entry?
Atmospheric conditions in confined spaces can change quickly, making it very important for you to continuously monitor their levels with a direct-reading portable gas monitor.
Direct-reading monitors, such as the Ventis® Pro5, not only tell workers whether the atmosphere in a confined space is safe, but also how safe. Is the oxygen concentration just barely above 19.5 percent, or is there enough margin for the entrant to work safely? The safest procedure is for all entrants to wear a direct-reading personal gas detector that continuously monitors for potential hazards.
You can improve safety even further by using connected monitors such as the Ventis® Pro5 or Radius® BZ1, enabling monitors to wirelessly share gas readings and alarms so the attendant always knows what is happening within the confined space. If conditions trend toward danger, workers will have the notice they need to safely exit the confined space.
If a monitor indicates dangerous levels of toxic gases, combustible gases, or oxygen deficiency (or enrichment), workers must evacuate the confined space, ventilate, and retest the atmosphere before re-entering.
What oxygen levels are safe for a worker entering a confined space?
With low oxygen being a significant cause of death in confined spaces, it’s important that you continuously measure oxygen levels.
OSHA dictates that the minimum "safe level" of oxygen in a confined space is 19.5 percent and the maximum is 23.5 percent.
If the oxygen concentration in a confined space surpasses 23.5 percent, the space is too oxygen-rich and could ignite combustible gases. On the other hand, low oxygen levels impair judgment and coordination. Extremely low levels of oxygen cause nausea, vomiting, and loss of consciousness. When oxygen levels are too low, that typically means another gas is displacing it. In these instances, it’s important to know what gas is displacing oxygen and why.
What are direct-reading portable gas monitors and why are they required for confined spaces?
Direct-reading monitors not only tell workers whether the atmosphere in a confined space is safe, but also how safe. Is the oxygen concentration just barely above 19.5 percent, or is there enough margin to work uninterrupted?
All of our gas detectors provide direct readings.
Safety laws require a pre-entry test just before a worker enters a confined space, and workers are only required to test again after leaving the space and preparing to reenter. Naturally, this leaves a lot of room for error if atmospheric conditions change while a worker is in the confined space, which is why confined space injuries and fatalities occur so frequently.
Periodic testing throughout the entry may be required if the confined space has a history of changing gas conditions. However, “periodic” leaves room for interpretation by workers or the company. A safer procedure is to arm all confined-space workers with direct-reading personal gas monitors and ask them to continuously monitor for gas hazards throughout the work period. If conditions begin to trend toward danger, workers will have the notice they need to safely exit the confined space.
If you rely on alarm-only monitors, this would not be possible. Because alarms are set to go off at predetermined thresholds, alarm-only instruments will not give workers a heads-up to potential dangers.
A direct-reading gas monitor, such as the Ventis® Pro5, displays gas levels so workers can see the exact reading, allowing them to make more informed decisions about whether entry is a wise choice and whether they can continue their work safely.
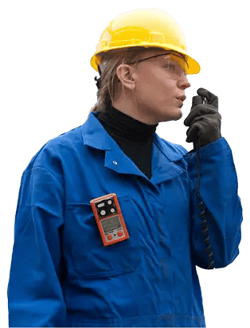